Applications For Fired Heaters
What follows are a few examples of applications for fired heaters.
Crude Furnace
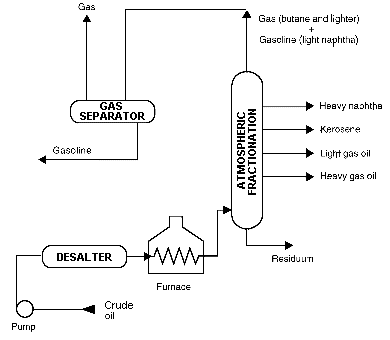
The first step in the refining process is the separation of crude oil into various fractions or “cuts” by distillation in atmospheric and vacuum towers. The main fractions or “cuts” obtained have specific boiling-point ranges and can be classified in order of decreasing volatility into gases, light distillates, middle distillates, gas oils, and residuum.
At the refinery, the desalted crude feedstock is preheated using recovered process heat. The feedstock then flows to a direct-fired crude charge heater where it is fed into the vertical distillation column just above the bottom, at pressures slightly above atmospheric and at temperatures ranging from 650° to 700° F (heating crude oil above these temperatures may cause undesirable thermal cracking). All but the heaviest fractions flash into vapor. As the hot vapor rises in the tower, its temperature is reduced. Heavy fuel oil or asphalt residue is taken from the bottom. At successively higher points on the tower, the various major products including lubricating oil, heating oil, kerosene, gasoline, and uncondensed gases (which condense at lower temperatures) are drawn off.
Catalytic Reformer Furnace
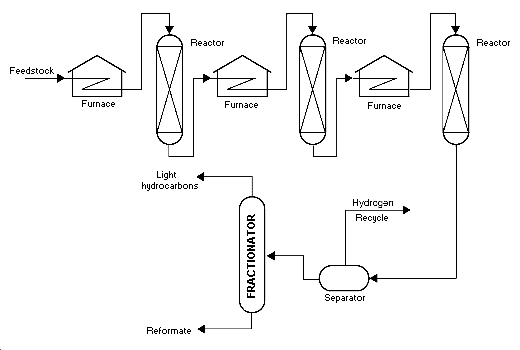
Catalytic reforming is an important process used to convert low-octane naphthas into high-octane gasoline blending components called reformate. Reforming represents the total effect of numerous reactions such as cracking, polymerization, dehydrogenation, and isomerization taking place simultaneously. Depending on the properties of the naphtha feedstock (as measured by the paraffin, olefin, naphthene, and aromatic content) and catalysts used, reformates can be produced with very high concentrations of toluene, benzene, xylene, and other aromatics useful in gasoline blending and petrochemical processing. Hydrogen, a significant by-product, is separated from the reformate for recycling and use in other processes.
Hydrocracker Furnace
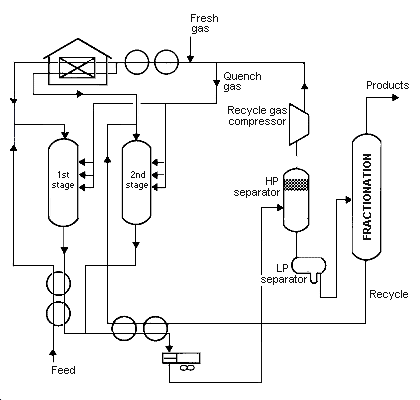
In the first stage, preheated feedstock is mixed with recycled hydrogen and sent to the first-stage reactor, where catalysts convert sulfur and nitrogen compounds to hydrogen sulfide and ammonia. Limited hydrocracking also occurs.
After the hydrocarbon leaves the first stage, it is cooled and liquefied and run through a hydrocarbon separator. The hydrogen is recycled to the feedstock. The liquid is charged to a fractionator. Depending on the products desired (gasoline components, jet fuel, and gas oil), the fractionator is run to cut out some portion of the first stage reactor out-turn. Kerosene-range material can be taken as a separate side-draw product or included in the fractionator bottoms with the gas oil.
The fractionator bottoms are again mixed with a hydrogen stream and charged to the second stage. Since this material has already been subjected to some hydrogenation, cracking, and reforming in the first stage, the operations of the second stage are more severe (higher temperatures and pressures). Like the outturn of the first stage, the second stage product is separated from the hydrogen and charged to the fractionator.
Visbreaker Furnace
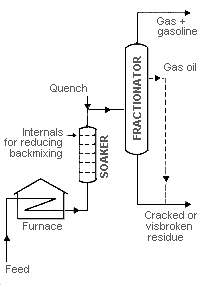
Visbreaking, a mild form of thermal cracking, significantly lowers the viscosity of heavy crude-oil residue without affecting the boiling point range. Residual from the atmospheric distillation tower is heated (800-950 degrees F) at atmospheric pressure and mildly cracked in a heater. It is then quenched with cool gas oil to control overcracking, and flashed in a distillation tower. Visbreaking is used to reduce the pour point of waxy residues and reduce the viscosity of residues used for blending with lighter fuel oils. Middle distillates may also be produced, depending on product demand. The thermally cracked residue tar, which accumulates in the bottom of the fractionation tower, is vacuum flashed in a stripper and the distillate recycled.
Vacuum Charge Heater
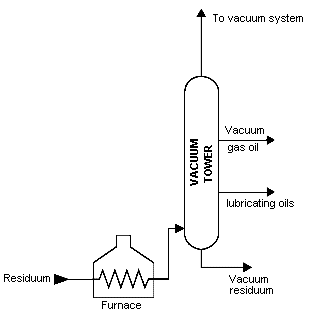
In order to further distill the residuum or topped crude from the atmospheric tower at higher temperatures, reduced pressure is required to prevent thermal cracking. The process takes place in one or more vacuum distillation towers. The principles of vacuum distillation resemble those of fractional distillation and, except that larger-diameter columns are used to maintain comparable vapor velocities at the reduced pressures, the equipment is also similar. The internal designs of some vacuum towers are different from atmospheric towers in that random packing and demister pads are used instead of trays. A typical first-phase vacuum tower may produce gas oils, lubricating-oil base stocks, and heavy residual for propane deasphalting. A second-phase tower operating at lower vacuum may distill surplus residuum from the atmospheric tower, which is not used for lube-stock processing, and surplus residuum from the first vacuum tower not used for deasphalting. Vacuum towers are typically used to separate catalytic cracking feedstock from surplus residuum.
Table of Applications
Refinery Process | Feedstock | From | Sub-Process | Typical products . . . . To |
---|---|---|---|---|
Atmospheric distillation | Crude | Desalting | Separation | Gases . . . . . . . . . . . . . Atmospheric distillation tower |
Naphtas. . . . . . . . . . . . Reforming or treating | ||||
Kerosene or distillates . . Treating | ||||
Gas oil . . . . . . . . . . . . . . Catalytic cracking | ||||
Residual . . . . . . . . . . . . Vacuum tower or visbreaker | ||||
Catalytic Reforming Process | Desulfurized naphtha | Coker | Rearrange, dehydrogenate | High octane gasoline . . Blending |
Aromatics . . . . Petrochemical | ||||
Naphthene-rich fractions | hydrocracker, hydrodesulfur | Hydrogen . . . . Recycle, hydrotreat, etc. | ||
Straight-run naphtha | Atmospheric fractionator | Gas . . . . . . . . Gas plant | ||
Visbreaking | Residual | Atmospheric tower & Vacuum tower | Decompose | Gasoline or distillate . . Hydrotreating |
Vapor . . . . . . . . . . . . Hydrotreater | ||||
Residue . . . . . . . . . . . Stripper or recycle | ||||
Hydrocracking | High pour point | Catalytic cracker, atmospheric & vacuum tower | Decomposition, hydrogenation | Kerosen, jet fuel . . . .Blending |
Gas oil | Vacuum tower, coker | Gasoline, distillates . . Blending | ||
Hydrogen | Reformer | Recycle, reformer gas . . Gas plant | ||
Vacuum Distillation | Residuals | Atmospheric tower | Separation | Gas oils . . . . . . . . Catalytic cracker |
Lubricants . . . . . . Hydrotreating or solvent | ||||
Residual . . . . . . . . Deasphalter, visbreaker, or coker |